In the modern era of automation, produzione intelligente, and Industry 4.0, industrial PCs have become the backbone of many critical operations. Whether you work in manufacturing, energy, trasporto, or any sector demanding reliable computing in harsh environments, industrial PCs are the trusted choice. But what exactly is an industrial PC, how does it differ from a regular PC, and why is it crucial for your industrial applications?
This comprehensive guide will demystify industrial PCs, explaining their features, uses, benefici, and future trends — helping you make informed decisions for your next project.
Cos'è un PC industriale?
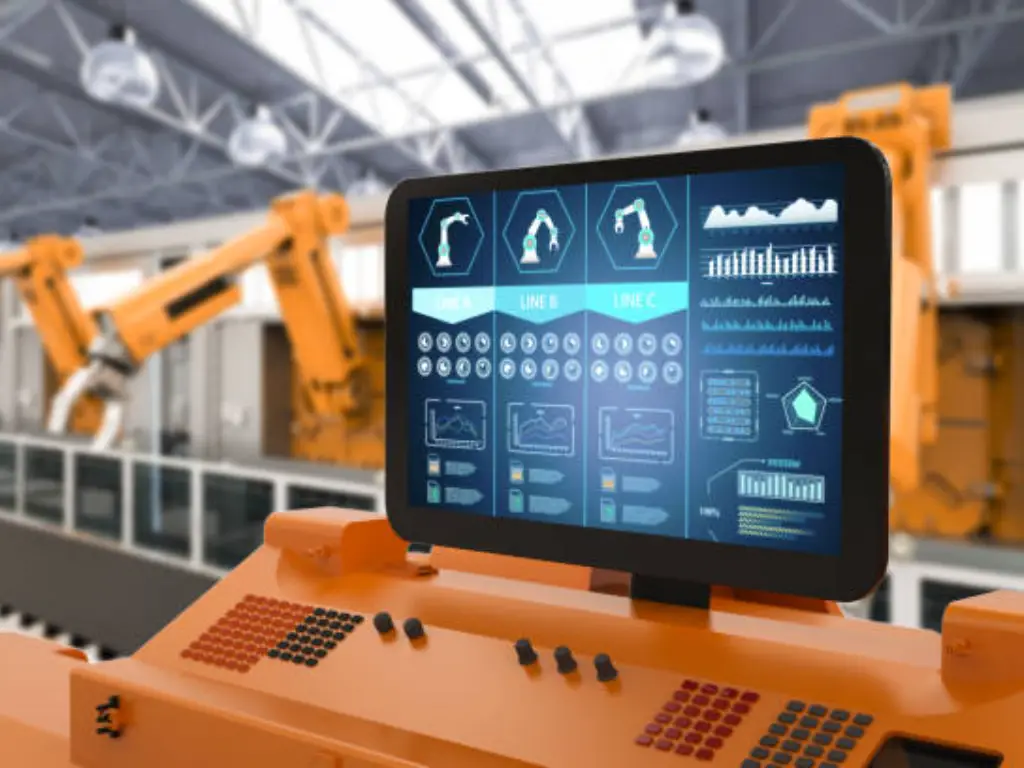
UN industrial PC (IPC) is a specialized computer designed to operate reliably in harsh industrial environments. It serves as the control center for a wide range of automated processes in industries like manufacturing, energy, trasporto, and logistics. Unlike standard consumer PCs, industrial PCs are built with industrial-grade components and housed in rugged enclosures to withstand extreme temperatures, umidità, polvere, vibrazione, and electrical noise.
Industrial PCs are often used in continuous operations that require long-term stability, affidabilità, and low maintenance. They’re also highly customizable, allowing integration with different industrial systems, interfacce, and mounting formats (per esempio., panel mount, rack mount, DIN rail).
Key Components of an Industrial PC:
- processore (Central Processing Unit): Manages all computing tasks, often optimized for low power and long lifecycle.
- RAM (Memoria): Temporary storage for active processes and real-time applications.
- Magazzinaggio (SSD or HDD): For storing the operating system, software, and machine data logs.
- Motherboard: Links all internal components, often with industrial-grade capacitors and connectors.
- Power Supply Unit: Designed for wide voltage input and stability under fluctuating conditions.
- I/O Ports: Includes USB, LAN, Com (RS-232/485), GPIO, or custom industrial protocols.
- Chassis and Cooling System: Rugged metal casing with passive (fanless) or active cooling.
In many cases, industrial PCs also integrate touchscreen displays for human-machine interface (HMI), improving usability in production environments.
How Does an Industrial PC Work?
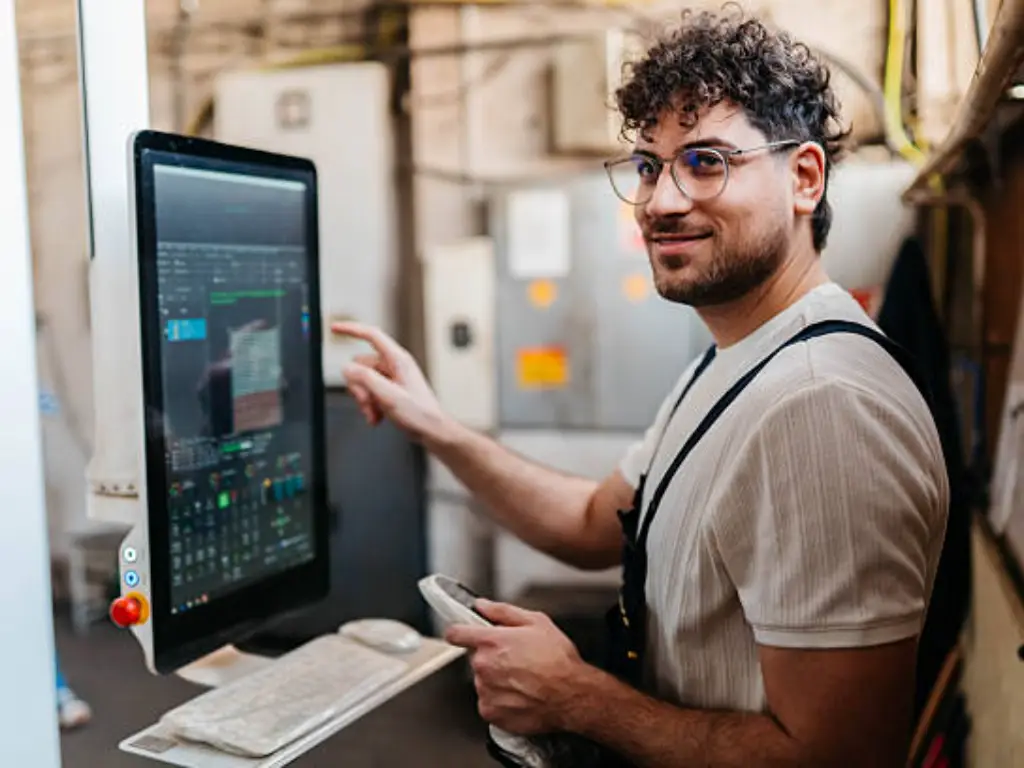
An industrial PC works by performing continuous data processing, controllare, and communication tasks — even under extreme operating conditions. Its role is to collect input signals, analyze data in real time, and issue output commands to other machines or systems based on predefined logic or software algorithms.
Here’s a simplified explanation of its working process:
- Input Collection: The IPC receives signals from connected devices such as sensors, scanner di codici a barre, PLC (controllori logici programmabili), or operator touchscreens.
- Data Processing: The CPU processes these inputs using the installed software, which may range from real-time operating systems (RTOS) to custom SCADA or automation control programs.
- Decision Making: Based on programmed logic or machine learning algorithms, the IPC determines what action should be taken — such as adjusting machine speed, triggering an alarm, or logging a value.
- Output Execution: The system sends output commands via its I/O ports to actuators, robotic arms, valves, rugged industrial displays, or cloud platforms for further processing or user interaction.
- Monitoraggio continuo: Industrial PCs are typically always-on, performing these cycles 24/7 with minimal downtime.
Industrial PC vs. Normal PC: Qual è la differenza?
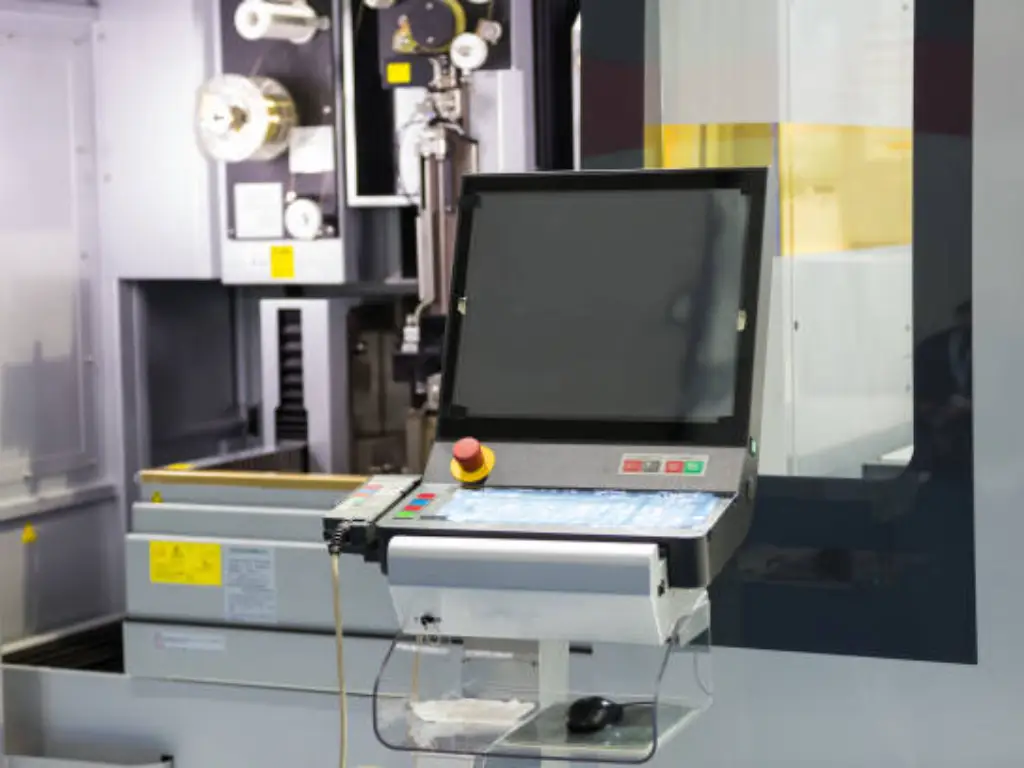
Industrial PCs and normal consumer PCs may share basic computing functions, but they differ widely in design, durabilità, and suitability for industrial environments. The table below offers a quick overview:
Caratteristica | Industrial PC | Normal PC (Consumer Grade) |
Durabilità | Rugged chassis, often IP-rated | Standard casing, not weatherproof |
Temperature Range | -40°C to 75°C | 0°C to 40°C typical |
Shock/Vibration Resistance | High, built for rough environments | Minimal resistance |
Cooling | Fanless or sealed cooling | Fan-based, dust-prone |
Power Supply | Wide voltage, surge protected | Standard 110/220V AC |
I/O Interfaces | Industrial ports (RS-232, CAN, eccetera.) | USB, HDMI, Ethernet only |
Lifecycle | Long-term availability (5–10 years) | Shorter upgrade cycles |
Opzioni di montaggio | DIN rail, panel, rack, VESA | Desktop or tower |
Key Differences Explained
1. Operating Temperature Range
Industrial PCs are often deployed in environments like outdoor control cabinets, hot factories, or cold storage facilities. Per questo motivo, many IPCs are built to operate reliably in a wide temperature range, typically from -20°C to +60°C, and in ruggedized models, even -40°C to 75°C. In contrasto, consumer-grade PCs are usually designed for office conditions, with optimal performance between 10°C and 35°C. Outside that range, component degradation or failure can occur due to overheating or condensation.
2. Resistance to Shock and Vibration
In factories, vehicles, or rail systems, continuous vibration can damage connectors, hard drives, and solder joints. Industrial PCs are often tested according to MIL-STD-810G standards, designed to withstand shocks up to 15G or vibrations of 5–500 Hz. They frequently use SSDs instead of HDDs and adopt fanless, solid-state cooling structures to minimize moving parts. In contrasto, consumer PCs are not validated for such conditions and can suffer mechanical failure from prolonged vibration.
3. Power Supply and Protection
Industrial PCs support wide input voltages (per esempio., 9–36V DC) and integrate protections like over-voltage, reverse polarity, and ESD filtering. This allows them to remain stable in environments with unstable power grids or machinery-induced noise. Consumer PCs rely on regulated AC power and can be damaged by voltage fluctuations.
4. Lifecycle and Component Availability
Consumer PCs often follow 12–18 month product cycles. In contrasto, industrial PC manufacturers commit to 5–10 years of component consistency to ensure long-term compatibility for deployed systems, especially critical in regulated sectors like medical or transportation.
Common Applications of Industrial PCs Across Industries
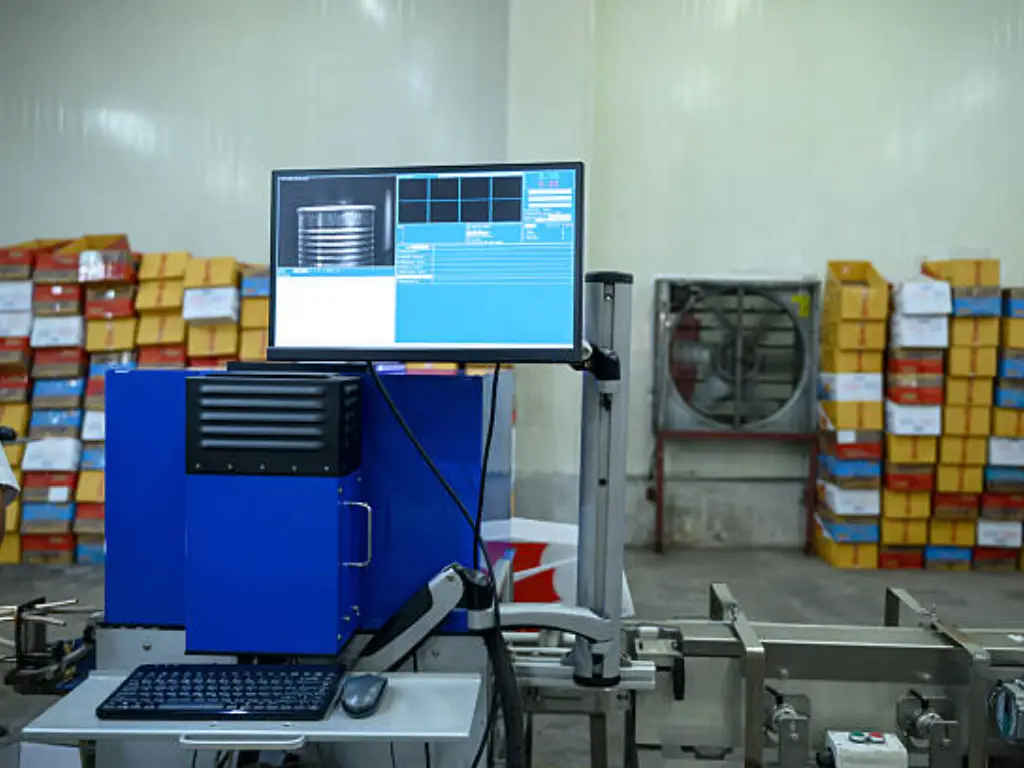
Industrial PCs serve as the digital brains behind many critical industrial operations. Alcune applicazioni comuni includono:
- Automazione industriale: IPCs control assembly lines, robotics, and CNC machines, processing sensor data and issuing commands to maintain production precision.
- Trasporto: From rail signaling to traffic management, industrial PCs monitor and control transportation infrastructure to enhance safety and efficiency.
- Energy and Utilities: IPCs manage power generation, grid distribution, and water treatment plants, often in remote and harsh environments.
- Oil & Gas and Mining: Rugged IPCs operate drilling rigs, monitor environmental conditions, and control extraction processes under extreme conditions.
- Assistenza sanitaria: Industrial PCs provide reliable control for imaging systems, diagnostic machines, and laboratory automation.
- Retail and Kiosks: Touchscreen industrial PCs enable interactive digital signage, chioschi self-service, and point-of-sale systems.
- Agriculture and Environmental Monitoring: IPCs collect and process data from sensors for precision farming and environmental tracking.
In all these applications, IPCs provide critical real-time processing, connettività, and human-machine interface capabilities that keep industrial operations running smoothly.
Benefits of Using Industrial PCs in Harsh Environments
When industrial operations take place in dusty factories, outdoor yards, or vibration-heavy vehicles, normal computers quickly fail. Here’s why industrial PCs are the preferred solution:
1. Reliable Operation in Extreme Conditions
Industrial PCs are designed for continuous use in environments with extreme heat, freezing temperatures, alta umidità, polvere, e vibrazione. Their rugged construction ensures system stability even when exposed to daily environmental stress, reducing the risk of unplanned downtime.
2. Reduced Maintenance Costs
Thanks to fanless cooling and sealed enclosures, these industrial rugged computers are less vulnerable to contaminants like dust or oil. This lowers the frequency of hardware failures and cuts the need for frequent cleaning or part replacements, saving long-term maintenance costs.
3. Enhanced Safety
In hazardous environments such as chemical plants or automated manufacturing lines, reliable equipment is critical. Industrial PCs minimize risks of short circuits, overheating, or connector failures, supporting a safer work environment.
4. Longevity and Future Proofing
With extended lifecycle support and compatibility with long-term OS versions, industrial PCs protect your system investment and reduce the risk of early obsolescence or costly re-certification.
5. Flexible Connectivity
Industrial PCs support a wide range of ports and protocols (per esempio., RS-232, Modbus, CAN), making it easy to connect with legacy machines, sensori, and modern control systems without additional converters.
6. Improved User Experience
Integrated industrial panels and customizable interfaces allow operators to interact directly with machines. This simplifies workflows, shortens training time, and improves on-site efficiency.
Come scegliere il diritto Rugged Industrial CompuTeR for Your Project
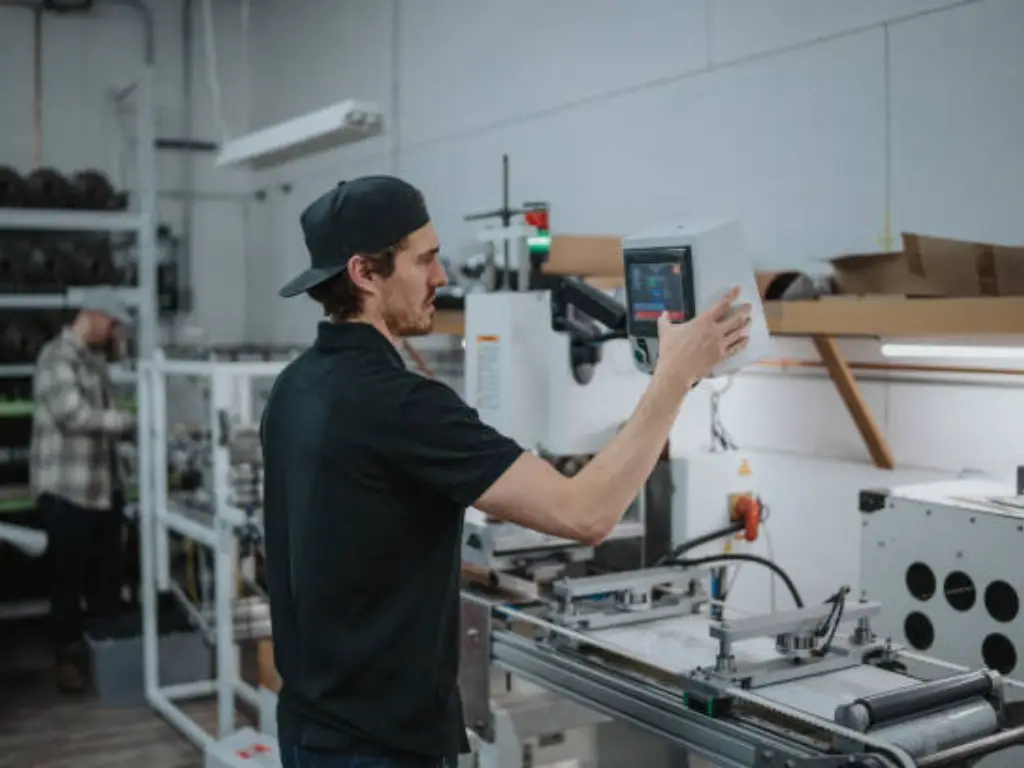
Selecting the right rugged industrial PC starts with understanding your operational environment and system requirements. Ecco 6 essential factors to guide your decision:
Environmental Tolerance
Determine whether the system will be exposed to dust, vibrazione, umidità, or extreme temperatures. Choose an IPC with the appropriate IP rating and certifications (per esempio., MIL-STD-810G) to ensure reliable long-term operation in harsh environments.
Performance Requirements
Assess your computing workload: Is it basic HMI visualization or complex real-time control? Select a processor and memory combination that meets performance needs without excessive power consumption or heat generation.
Connectivity and Expansion
Define what ports and communication protocols you need—USB, serial (RS-232/485), CAN bus, Ethernet, or wireless. For future flexibility, look for systems that support expansion via PCIe, mini-PCIe, or M.2 slots.
Integrated Display Options
If operator interaction is required, opt for models with industrial-grade touchscreens. Consider screen size, risoluzione, and touch type (per esempio., resistive or capacitive). As a professional industrial-grade touchscreen manufacturer, we provide customizable industrial display solutions built to withstand demanding conditions.
Power and Stability
Ensure the PC supports wide-range DC input (per esempio., 9–36V) and includes protections such as surge resistance and reverse polarity safeguards—crucial for unstable or mobile power sources.
Software Compatibility and Lifecycle Support
Verify support for your preferred OS, such as Windows IoT, Linux, or RTOS. Also consider vendors offering long-term hardware availability and update support to reduce integration risks over time.
Future Trends in Industrial PC Technology
As industries evolve with digital transformation and smart automation, industrial PCs continue to innovate. Key future trends include:
1. Edge Computing and AI Integration
Industrial PCs will increasingly incorporate AI processors and edge computing capabilities to analyze data locally, reducing latency and bandwidth needs.
2. Enhanced Connectivity with 5G and IIoT
Support for 5G networks and Industrial Internet of Things (IIoT) protocols will enable faster, more reliable communication among industrial devices.
3. More Compact and Energy-Efficient Designs
Advances in component miniaturization and power-saving technologies will produce smaller IPCs with higher performance and lower energy consumption.
4. Advanced Security Features
With increased connectivity, cybersecurity will become paramount. Industrial PCs will embed hardware-level security measures to protect critical infrastructure.
5. Modular and Scalable Architectures
Future IPCs will be highly modular, allowing users to easily upgrade CPUs, magazzinaggio, and I/O to extend system lifespan.
6. Improved Human-Machine Interfaces (HMI)
Touchscreens will be complemented by voice control, riconoscimento dei gesti, and augmented reality overlays to enhance operator interaction.
Staying abreast of these trends helps industries leverage industrial PCs to maximize operational efficiency and future-proof their infrastructure.
Domande frequenti
Q1: Can I use a regular PC instead of an industrial PC?
While technically possible, regular PCs lack the ruggedness and reliability required in harsh industrial environments, leading to higher failure rates and downtime.
Q2: Are industrial PCs compatible with standard Windows or Linux OS?
SÌ, many IPCs run embedded versions of Windows or Linux, optimized for stability and long-term support.
Q3: How long do industrial PCs typically last?
With proper maintenance, IPCs can operate reliably for 5 A 10 years or more, far exceeding the typical lifespan of consumer PCs.
Q4: Can industrial PCs be customized?
SÌ, most manufacturers offer customization for chassis, I/O ports, display options, and software to fit specific industrial needs. A TouchWo, we provide fully customizable industrial all-in-one PCs with touchscreen displays ranging from 5 pollici a 110 pollici, tailored to meet the demands of diverse applications and environments.
Q5: What is the difference between PLC and industrial PCs?
PLCs are dedicated controllers designed for real-time automation tasks with rugged I/O modules. Industrial PCs offer more computing power and flexibility, supporting complex software like HMI and data analysis. PLCs suit simple control and safety-critical tasks, while industrial PCs handle advanced processing and integration needs.